Winds of change for glass
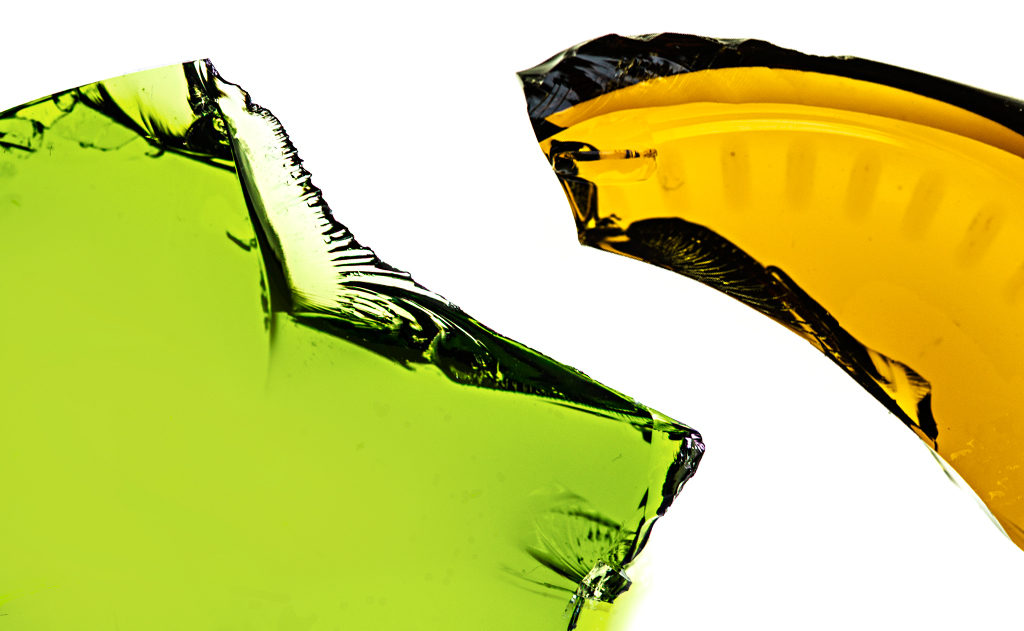
EPR for packaging came into force at the beginning of May. As a result of this responsibility for organising the take-back and recycling of consumer packaging will gradually be transferred from municipalities to producer organisations. The producer organisation for non-deposit glass packaging, Suomen Keräyslasiyhdistys ry (SKY), has outsourced the take-back and recycling of glass to PYR Ltd.
“The producer organisations in the packaging sector, namely Suomen Kuitukierrätys Oy (SUK) for fibre packaging, Suomen Uusiomuovi Oy (SUM) for plastic packaging, Mepak-Kierrätys Oy for metal packaging and SKY for glass packaging, have jointly transferred the organisation of consumer packaging take-back to PYR. In contrast to other producer organisations, however, SKY feels that it makes sense to outsource the entire chain from take-back to recycling to one operator,” says SKY’s managing Director, Maija Peltola, adding that PYR was considered to be the natural choice as cooperation partner since the company represents the same operators as the producer organisations do. Suomen Palautuspakkaus Oy (www.palpa.fi) will retain responsibility for the entire recycling process for deposit glass bottles.
Thirty eight reception terminals for glass packaging waste
“As SKY has transferred the practical implementation of glass take-back and recycling to PYR, we are planning, inviting tenders and making contracts with various operators in the field. Operational activities will be bought in. Our task is to ensure that the entire scheme works efficiently and provides quality results,” says PYR’s CEO, Juha-Heikki Tanskanen.
From the beginning of May 38 reception terminals throughout Finland started to accept free of charge the consumer glass packaging waste collected by municipalities and waste haulage firms. The regional reception terminals, operating as transfer loading stations, are situated in the vicinity of existing waste reception centres. PYR invited tenders for reception terminal services and contracts were signed in time for the beginning of May. Tanskanen further explains, “The greatest challenge in establishing a countrywide network of reception terminals for discarded glass packaging has been the tight schedule. The Packaging and Packaging Waste Decree only came into force in summer 2014, and this is a question of countrywide operations.”
Glass packaging waste converted into new packaging in the UK
“Glass packaging is no longer manufactured in Finland, which means that the only domestic recycling options are in the manufacture of foam glass and glass wool. Glass packaging waste collected from consumers and delivered for recycling cannot be used in the manufacture of glass wool as it does not meet the purity requirements and even after cleaning it mainly goes to other locations in Europe to be recycled. There is demand for glass packaging waste in other parts of Europe,” says Peltola.
The UK based firm, URM UK Ltd T/A Berryman (www.berrymanglassrecycling.com), has been selected as the operator to treat non-deposit glass packaging waste. In future glass packaging waste will be transported mainly to Berryman’s glass treatment plant in Knottingley. From this plant the treated and sorted glass material will be delivered to a glass packaging production facility to be manufactured into bottles and jars for applications in the food industry. Berryman was selected through public tendering.
“Two critical factors influenced SKY’s and PYR’s decision: cost and the fact that discarded glass packaging will be forwarded as raw material for the manufacture of new glass packaging. In 2014 Berryman was granted End of Waste (EoW) status by the EU. This means that the glass treated by the firm and sold to its industrial customers is not classified as waste. Berryman was a cost-effective option for us,” reasons Tanskanen.
Glass packaging waste must fulfil recycling quality standards
The Packaging and Packaging Waste Decree requires that the quantity of recycled glass packaging waste will be raised from its present level by 2020.
According to Peltola, previously larger quantities of glass have been collected than have been delivered for recycling as glass was also used in building and construction applications.
“After the responsibility for collection has been transferred to producer take-back, the use of glass in civil engineering will for the main part be discontinued and the quantity of glass packaging waste to be recycled will grow. It is necessary that the material in take-back is sorted according to the instructions issued by producers. The producers’ sorting instructions can be found on PYR’s website,” says Peltola.
Uniform sorting instructions must be implemented
In Peltola’s opinion, it is important that glass packaging waste is sorted according to uniform instructions throughout the whole of Finland. The majority of municipalities have issued instructions for sorting glass packaging waste in accordance with producers’ instructions, but there are still municipalities whose instructions differ from those of the producers.
“SKY’s aim is that the take-back and recycling of glass packaging waste functions efficiently under the new scheme, legal recycling requirements are met and producers’ recycling fees are kept in check. It is also important that consumers are informed about the sorting instructions for glass and that they know where the nearest take-back point is located,” Peltola points out.
Efficient treatment of glass packaging waste
Berryman treats the glass in several phases.
- Quality check: If incoming glass packaging waste does not meet quality standards, it is separated and can be used for other purposes or it is rejected.
- Pre-processing: Impurities, such as plastic, are removed from the glass packaging waste. The larger pieces of cullet are broken down so that such items as aluminium caps or the neck rings on bottles can be removed.
- Drying: Labels and residues of paper and dust are removed by drying.
- Sorting: Glass cullet is sorted according to size and the smallest fraction is rejected. Ceramic residue, stones, grit, metal and lead glass are removed, after which the cullet passes through colour-sorting equipment. The cullet is sorted into green, brown and clear cullet.
- Storage: The three colours of cullet are stored separately and tested so that the batches comply with customer quality standards.
The finished cullet, treated and sorted at Berryman’s Knottingley plant, is delivered to the nearby Ardagh Group glass packaging manufacturing facility. Here the material is processed to make new glass packaging for such firms as Heineken, Pernod Ricard, Bacardi Martini, Heinz, Nestlé, Unilever and Coca Cola.
Over the past few years Berryman has invested GBP 5 million in cutting-edge, colour-sorting technology at its glass treatment plant in Knottingley, Yorkshire. It can sort coloured glass waste into three separate colour streams achieving over 80 per cent accuracy. Berryman operates to ISO 9001 standards.